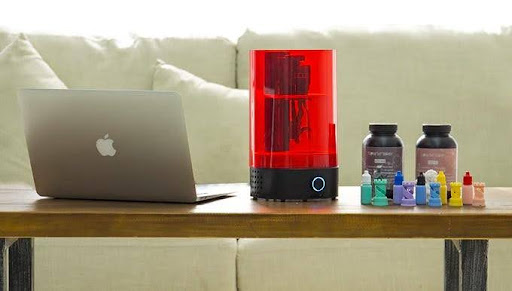
Sparkmaker SLA 3D Printer/Courtesy: Sparkmaker3D
Stereolithography Apparatus (SLA) was the first 3D printing technology ever to be invented. It was patented by Charles Hull, an American engineer, and now regarded as the ‘Father of 3D Printing’.
He applied for the patent in 1984, was granted the same in 1986, and the technology was commercialized by 1988. The technology was developed to be a tool for rapidly manufacturing prototypes but over the years the technology has evolved into a robust manufacturing technology to produce even end-use parts.
ABOUT SLA 3D PRINTING TECHNOLOGY
Stereolithography Apparatus (SLA) or simply Stereolithography falls under the Vat Photopolymerization category of 3D printing technology as defined by ASTM. Stereolithography uses a laser to cure a vat full of liquid resin to form a three-dimensional object. The unique combination of the liquid material and laser has a significant impact on the surface finish of the 3D printed object and in this article, we will see how the technology is operated, its components, the materials used, and its popular applications.
-
- Printed Part: This is the actual 3D printed part
- Supports: The necessary support features added to the design to print overhangs and other fine features
- Resin: This is the liquid resin material that is cured to form the solid three-dimensional object
- Build Platform: The platform onto which the part is printed
- Laser: The UV light in the form of a laser is used to cure the liquid resin
- Galvanometer: The laser is directed onto the resin using a set of mirrors called as a Galvanometer
- X-Y Scanning Mirrors: The scanning mirrors are responsible for flashing the laser onto the resin. This helps in tracing the cross-sectional geometry of the model
- Resin Tank: This is a tank filled with the liquid resin material
Sweeper Blade: This sweeper blade sweeps through the resin tank after completion of each layer
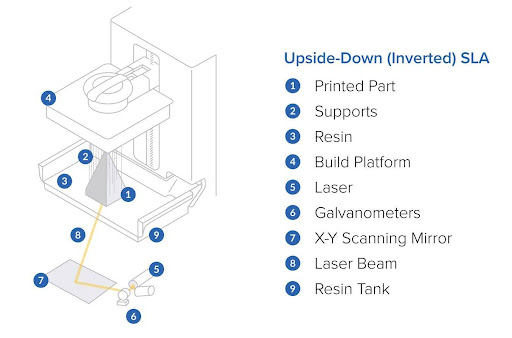
Components of an SLA 3D Printer/Courtesy: Formlabs
DESIGN GUIDE – STEREOLITHOGRAPHY APPARATUS (SLA)
WORKING OF AN SLA 3D PRINTER
Below we explain the working of an SLA 3D printer. Kindly note that the explanation is for an upside-down SLA 3D printing technique:
- At the start of the print, the build platform is immersed in the tank of liquid photopolymer. The immersion distance is equal to one layer height.
- The process then starts with the UV laser being directed through the scanning mirrors onto the liquid resin at specifically defined points. The laser-liquid interface points are cured (hardened), i.e., they turn from liquid to solid. This curing continues for the entire layer as each point is exposed to the laser.
- When the first layer is cured, the build platform moves up by a safe distance. The sweeper blade then sweeps through the resin tank to stabilize the resin and also remove air bubbles, if any. Then once the blade completes the sweeping action, the build platform moves down into the resin tank again and the 3D printing process is carried out similarly as the first layer.
- It is important to note that for the first layer, the build platform is the base layer while from the second layer onwards the previous layer acts as the base layer on top of which the new layer is printed.
- Once the printing completes, the part is considered to be in a green state that means it is still not completely cured. So this part is allowed to remain on the build platform, till excess resin is dripped. After that, the model is removed from the build platform, is put through a cleaning process, and then subjected to more UV light in a dedicated UV Curing chamber.
- This post-printing UV curing helps the object to achieve its highest possible mechanical and thermal properties. And thus here the process finally completes.
MATERIALS – STEREOLITHOGRAPHY APPARATUS (SLA)
MATERIALS USED IN SLA 3D PRINTING
SLA 3D printing technology uses liquid thermoset polymer materials in a liquid form. These photopolymers are more brittle than thermoplastics used in FDM & SLS technologies and so they are generally avoided to be used for functional prototypes that will undertake significant loading.
Stndard Resin
The resin to get you started with SLA 3D printing. The standard resin produces smooth parts, it exhibits an injection mold-like surface finish however it is brittle and thus used for non-functional parts.
Multiple models made from Standard resin/Courtesy: Formlabs
Clear Resin
The clear resin is formulated for specific applications falling under optics, lighting, and applications requiring translucent parts. It can be called as a popular variant of the standard resin as its properties are comparable to the standard resin.
Vehicle headlight with clear resin/Courtesy: 3D Systems
Castable Resin
Castable resin is used by jewelers for making customized products for their clients. It helps the jewelers to rapidly create custom designs, their prototypes for try-on and then convert them into precious metals through investment casting.
Castable resins are also used for smaller mold-making applications.
Jewelry models before and after casting/Courtesy: Formlabs
High-temperature Resin
This is an application-specific resin formulated only for products required to sustain very high temperatures.
Flexible Resin
It is not difficult to figure out the use of flexible resins. With flexible resins, manufacturers can make flexible or elastic parts for various applications like anatomical models, props and models, grips and handles, seals and gaskets, vibration-damping parts, etc.
Shoe sole made from flexible resin/Courtesy: Formlabs
Bio-compatible resin
These represent the FDA-approved materials that are compatible to be used for applications requiring long-term skin and mucosal membrane contact. Applications of the biocompatible resins include surgical planning and implant sizing tools, medical devices, intra-oral guides, jigs and fixtures, and for research and development activities.
APPLICATIONS OF SLA 3D PRINTING TECHNOLOGY
Prototyping
Just like every 3D printing technology, SLA 3D printing too can be used for making prototypes. Since SLA 3D printing achieves the smoothest surface finish of all the technologies, it can be used to create form and fitment testing, or look and feel testing prototypes.
Manufacturing
SLA 3D printing also has applications at various stages of the manufacturing process. Right from the pre-production to the post-production the applications are only limited by one’s imagination.
Popular applications like rapid prototyping and manufacturing validation parts to jigs and fixtures and tooling and even batch-scale end-use product manufacturing.
Drill jig/Courtesy: Formlabs
Healthcare
Healthcare is also one of the earliest adopters of the SLA 3D printing technology. The medical industry is using the technology to create pre-surgical models, models for mock surgeries, medical device development, custom tools for conducting surgeries and operations, and much more.
The recent example being the use of SLA 3D printing to make the Nasopharyngeal swab required for collecting samples for Covid-19 tests.
Nasopharyngeal swab/Courtesy: Formlabs
Dentistry
The dental industry has been one of the earliest adopters of the SLA 3D printing technology. It revolutionizes the supply chins of dentistry by rapidly manufacturing custom-fitting crowns and bridges, surgical guides, dentures, aligners, and more right on-demand. It drastically reduces the time taken to manufacture such parts, they can be manufactured right in front of the patient and also reduces the overall cost. A win-win for everyone.
Dental models/Courtesy: 3D Systems